
There is a wide range of heat-resistant plastics applications due to their properties, such as low cost, lightweight, and ease of processing. From machining and fabrication to 3D printing, plastics are an excellent option for many projects. However, not all plastics are suitable if your project requires the material to withstand harsh environments with high temperatures. Do not worry; we can think of a few that will be up to the task. These materials have excellent thermal properties.
In this article, we will examine five reliable heat-resistant plastics: Polyetherimide (PEI), Polyamide (PA), Polytetrafluoroethylene (PTFE), Polycarbonate (PC), and Polyetheretherketone (PEEK). We’ll discuss amorphous vs. semi-crystalline plastics, some common thermal properties, and how to choose which is right for your project.
What is a heat-resistant material?
Heat-resistant plastics can handle high temperatures without losing their strength or shape. These materials stay strong and valuable even when hot, making them great for situations where heat is a factor. Some common heat-resistant plastics are polyimide, polyphenylene sulfide, and polyether ether ketone (PEEK).
Plastics: Amorphous vs. Semicrystalline
Plastics fall into two categories, determining how they react when exposed to elevated temperatures. Understanding amorphous and semi-crystalline plastics can help decide which type best suits your project’s unique challenges.
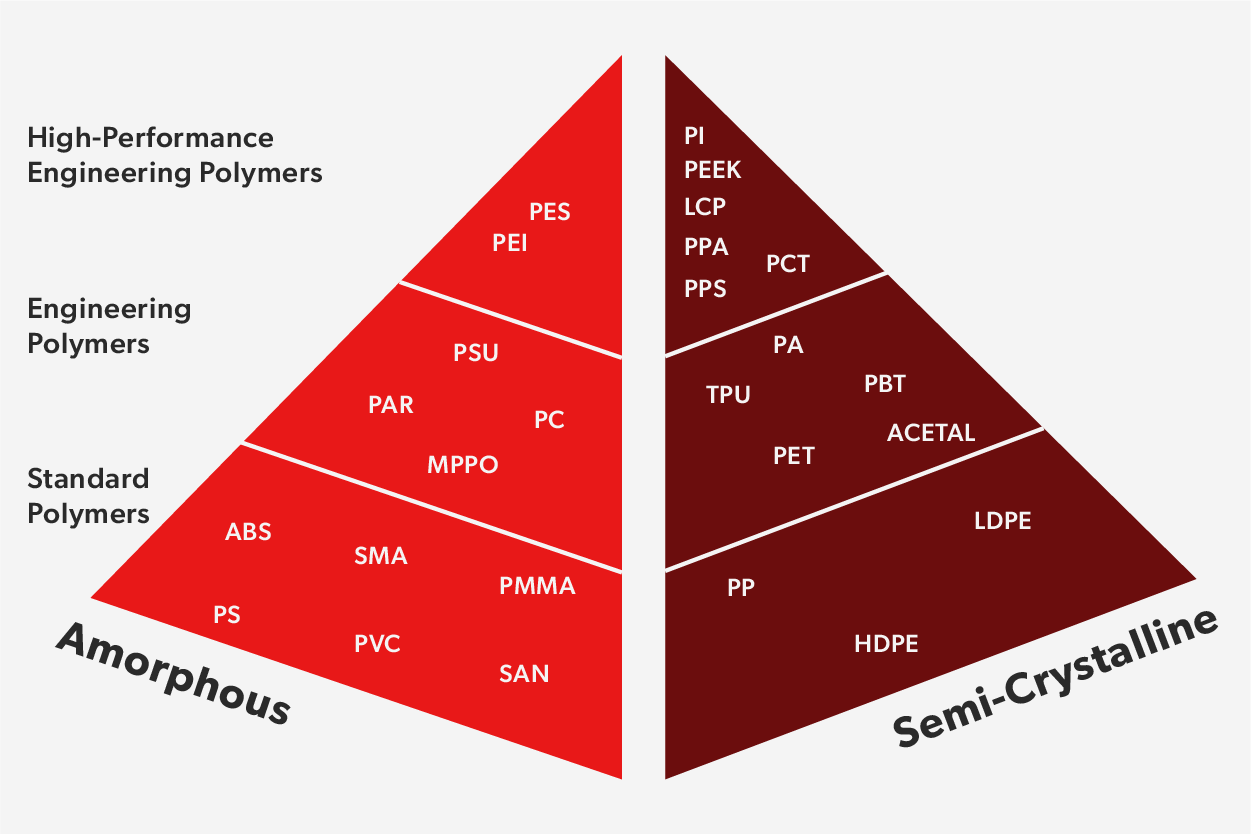
Amorphous Plastics
Amorphous plastics, or non-crystalline plastics, are a type of polymer without a clear structure. These materials have unique qualities, including transparency, resistance to impact, and the ability to process quickly at higher temperatures. Instead of melting at a specific point, they soften as heated.
Polystyrene (PS), polycarbonate (PC), polyetherimide (PEI), and polyvinyl chloride (PVC) are examples of amorphous plastics.
Semi-Crystalline Plastics
Semi-crystalline plastics have a mainly ordered molecular structure. These plastics contain ordered crystalline areas mixed with unordered, random parts. These plastics change from solid to liquid at a precise melting point. Because of this, semi-crystalline plastics are the most common materials used to make fibers, films, blends, and composites.
Polyethylene (PE), polyethylene terephthalate (PET), polytetrafluoroethylene (PTFE), and polypropylene (PP) are some examples of semi-crystalline plastics.
Heat-Resistant Plastics Thermal Properties
When it comes to high-performance applications, heat-resistant plastics are a critical material choice. These specialized polymers can withstand extreme temperatures and harsh environments, making them ideal for various industries.
This section will explore the key thermal properties that define heat-resistant plastics and why they are essential.
Continuous Operating Temperatures
Many heat-resistant plastics’ ability to operate continuously at temperatures up to 300°C or higher is not just a feature. It’s crucial to determine their suitability for continuous-use applications where consistent performance is vital.
Flame Resistance
In addition to their thermal stability, heat-resistant plastics often exhibit excellent flame resistance. This property reduces fire risk and ensures safety in high-heat environments, providing a reassuring layer of protection.
Glass Transition Temperature
The glass transition temperature (Tg) marks where a plastic transitions from a rigid, glassy state to a more flexible, rubbery state. Heat-resistant plastics typically have high Tg values. This property preserves their mechanical properties even at elevated temperatures.
Heat Deflection Temperature
The heat deflection temperature (HDT) measures a plastic’s ability to resist deformation under a specified load at elevated temperatures. High HDT values ensure heat-resistant plastics can reliably perform in demanding applications.
Melting Point
Heat-resistant plastics boast exceptionally high melting points, ranging from 300°C to 400°C or more. This property ensures they maintain their structural integrity and dimensional stability even under intense heat, providing security about their performance in demanding applications.
Heat-Resistant Plastic Materials
Reliability is very important when choosing materials that can handle high temperatures. Heat-resistant plastics are key in aerospace, automotive, and electronics industries because they perform consistently. These plastics do not bend when exposed to heat and keep their strength, making them a reliable choice.
Here are five examples of heat-resistant plastics:
1. Polyetherimide (PEI)
Polyetherimide (PEI) is a strong plastic that can withstand high temperatures. Due to its heat resistance, strength, and ability to keep shape, it can handle temperatures up to about 217°C (423°F) without losing strength. Additionally, PEI is flame-resistant and produces low smoke, making it safer for applications that prioritize safety.
Key Properties:
- High heat resistance
- Excellent dimensional stability
- Outstanding mechanical properties
- Inherent flame retardancy
- Exceptional chemical resistance
- Low moisture absorption
- Easy to machine and fabricate
Applications:
- Aerospace parts (e.g., aircraft interiors, engine components)
- Medical devices (e.g., surgical instruments, prosthetics)
- Electrical/electronics enclosures (e.g., circuit breakers, junction boxes)
- Industrial equipment (e.g., pumps, valves, gears)
- Consumer products (e.g., kitchen appliances, power tools)
2. Polyamide (PA)
Nylon, or polyamide, is a flexible and strong plastic material. It is well-known for its ability to resist heat. Some types can withstand up to 150°C (302°F) without losing strength. Because of these qualities, many industries use nylon, where durability and performance are essential.
Key Properties:
- Heat resistant
- High strength and rigidity
- Excellent wear and abrasion resistance
- Good chemical resistance
- Low coefficient of friction
- High impact strength
- Dimensional stability
- Ease of fabrication
- Lightweight
Applications:
- Automotive parts (e.g. gears, bearings, fuel system components)
- Electrical and electronic components (e.g. connectors, housings, insulation)
- Consumer goods (e.g. sports equipment, toys, household items)
- Industrial machinery parts (e.g. gears, bearings, pulleys)
- Medical devices (e.g. implants, prosthetics, surgical instruments)
- Aerospace components (e.g. structural parts, interior fittings)
- Packaging and containers (e.g. bottles, caps, lids)
3. Polytetrafluoroethylene (PTFE)
Polytetrafluoroethylene (PTFE) is a synthetic material known for its low friction and heat resistance. It can withstand temperatures up to 260°C (500°F) without losing strength. Due to its chemical resistance, PTFE is suitable for demanding environments.
Key Properties:
- Heat resistant
- High chemical resistance
- Excellent thermal stability
- Low coefficient of friction
- Non-stick surface
- Electrical insulation properties
- Resistant to weathering and UV exposure
- Hydrophobic and oleophobic
- Biocompatible and non-toxic
- Extremely low permeability
- Maintains properties over a wide temperature range
Applications:
- Chemical processing equipment
- Semiconductor manufacturing
- Electrical insulation
- Cookware and bakeware
- Plumbing tapes and gaskets
- Aerospace and automotive components
- Medical devices and implants
- Textiles and fabrics
- Lubricants and coatings
- Outdoor gear and equipment
4. Polycarbonate (PC)
Polycarbonate (PC) is a strong and versatile plastic known for its durability and clear appearance. Polycarbonate can handle high temperatures, staying strong at up to 135°C (275°F). Its heat resistance and lightweight design make it suitable for many industries, such as automotive, electronics, and construction, where safety and clarity are essential.
Key Properties:
- Heat resistant
- High chemical resistance
- Excellent thermal stability
- Low coefficient of friction
- Non-stick surface
- Electrical insulation properties
- Resistant to weathering and UV exposure
- Hydrophobic and oleophobic
- Biocompatible and non-toxic
- Extremely low permeability
- Maintains properties over a wide temperature range
Applications:
- Chemical processing equipment
- Semiconductor manufacturing
- Electrical insulation
- Cookware and bakeware
- Plumbing tapes and gaskets
- Aerospace and automotive components
- Medical devices and implants
- Textiles and fabrics
- Lubricants and coatings
- Outdoor gear and equipment
5. Polyetheretherketone (PEEK)
PEEK, or polyether ether ketone, is one of the strongest thermoplastics. It can withstand temperatures up to 143°C (289°F) without losing strength and melts at 343°C (649°F).
PEEK is ideal for challenging aerospace, automotive, medical devices, and chemical processing applications. Its durability and resistance to heat and chemicals make it effective where other materials fail. Engineers and manufacturers choose PEEK for its performance and reliability.
Key Properties:
- Heat resistant
- High strength and stiffness
- Excellent chemical resistance
- Outstanding thermal stability
- Inherent flame retardancy
- Biocompatibility and sterilizability
- Dimensional stability
- Low coefficient of friction
- Wear and abrasion resistance
Applications:
- Medical devices and implants
- Aerospace and aviation components
- Automotive and transportation parts
- Electrical and electronics applications
- Chemical processing equipment
- Oil and gas industry components
- Semiconductor manufacturing tools
- Food processing equipment
- Sporting goods and outdoor gear
FAQs
ABS plastic can handle moderate heat, making it suitable for many uses.
Acrylic plastic can resist moderate heat at temperatures up to 200°F (93°C) without changing shape or breaking down.
PET plastic also handles moderate heat well.
Polycarbonate is very heat resistant, which makes it a strong material.
Polypropylene is a plastic type with good heat resistance, making it useful for moderate temperatures. Its melting point is between 320°F and 338°F (160°C to 170°C).
Adding glass fibers to plastic can significantly improve its heat resistance. This additive makes the plastic better for high-temperature use. The glass fibers help strengthen the plastic and stabilize it under heat.