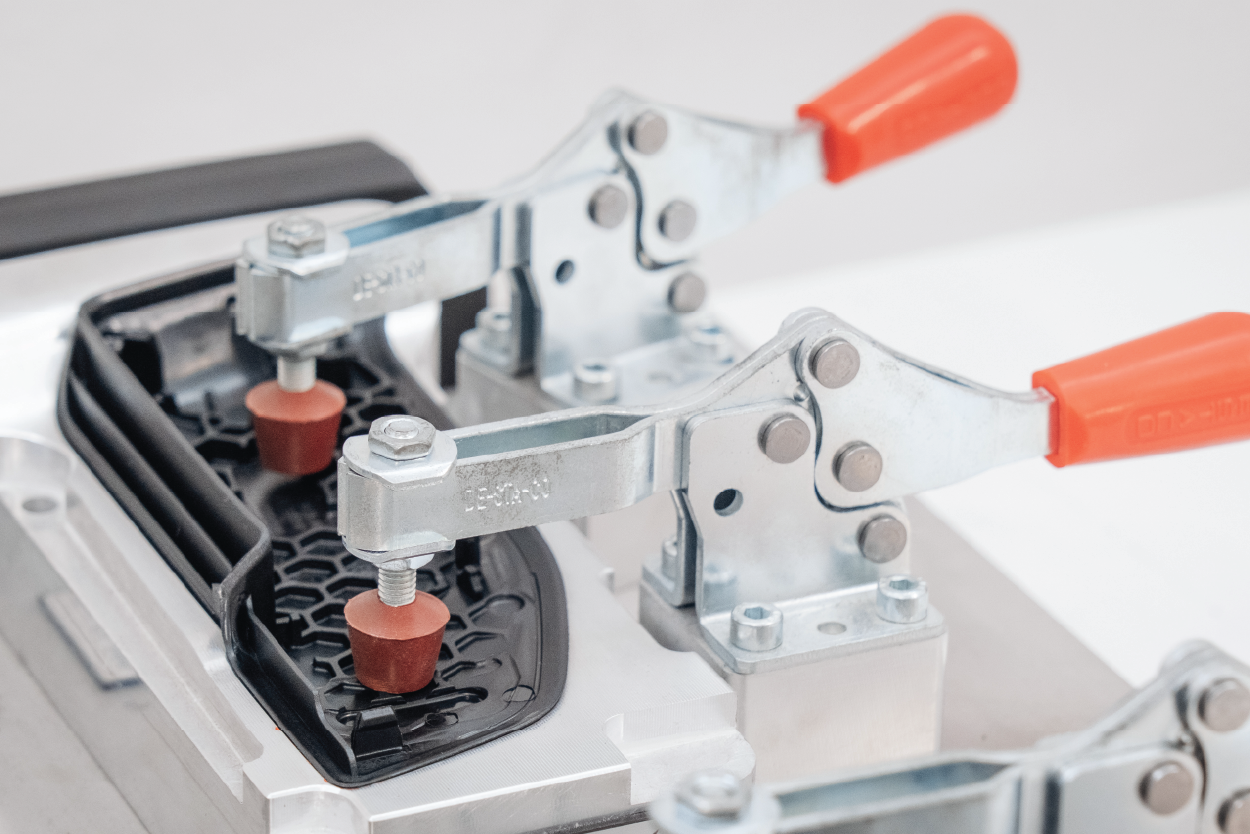
Understanding the unique roles of jigs and fixtures and how to use them effectively can enhance your manufacturing capabilities. This post will examine the differences between these two essential tools, providing insights that can help you improve your production process and ensure consistent, high-quality results.
What are Fixtures?
Fixtures play a critical role in the manufacturing process, particularly in maintaining the high product quality that customers expect. They accurately hold and position workpieces during fabrication. Making sure each part meets the required standards. Due to this, fixtures are tools and reliable quality assurance partners.
Types of Fixtures
Turning Fixtures
Turning fixtures are not just crucial, but also versatile tools in manufacturing. They securely hold and position workpieces during turning, providing a stable base for accurate machining. This versatility allows them to efficiently produce a wide range of turned components, making them indispensable for handling diverse manufacturing needs.
Milling Fixtures
Milling fixtures are essential tools in the milling process. They hold workpieces securely and position them correctly during machining. These fixtures provide a stable platform, keeping the workpiece steady and aligned with the cutting tool. Milling fixtures come in different types, including vises, clamps, and specialized jigs, to fit various shapes and machining needs. By using milling fixtures, manufacturers can produce consistent, high-quality results, boost productivity, and improve the efficiency of their milling operations.
Broaching Fixtures
A broaching fixture is a tool used in manufacturing to create complex shapes inside and outside a workpiece. It has cutting teeth lined up in a row that moves through the material, removing small pieces with each pass to create the desired shape. Industries like automotive, aerospace and industrial machinery commonly use broaching fixtures to make gears, splines, keyways, and other detailed features accurately and consistently.
Grinding Fixture
A grinding fixture is a tool that holds a workpiece securely during grinding. It ensures the workpiece’s position is accurate, which allows for precise material removal and achieves a smooth surface finish. Different grinding fixtures are available to fit various part shapes and grinding needs. They provide a stable platform for effective and high-quality grinding work.
Boring Fixtures
Boring fixtures are essential to the manufacturing process. They provide a stable and secure platform for workpieces during machining. These fixtures help position and align parts accurately, leading to consistent and precise production. By using dull fixtures, manufacturers can improve workflows, enhance part quality, and boost overall efficiency.Boring fixtures are essential components in the manufacturing process, providing a secure and stable platform for workpieces during machining operations. These fixtures ensure precise positioning, alignment, and support, enabling consistent and accurate production. By utilizing boring fixtures, manufacturers can optimize their workflows, improve part quality, and enhance overall efficiency in their operations.
Tapping Fixtures
Tapping fixtures are devices that hold parts securely while tapping threads. They create a stable platform that helps form accurate threads and reduces the chances of tap breakage or part distortion. These fixtures are standard in CNC machining and manufacturing environments where consistent, high-quality tapped holes are essential.
Duplex Fixtures
Duplex fixtures are tools used in manufacturing to machine or process two identical parts simultaneously. They increase productivity and efficiency by producing two components together rather than one at a time. Industries like automotive, aerospace, and general manufacturing often use duplex fixtures for high-volume production. With this innovative design, Prototek helps clients improve their manufacturing workflows and increase their output.
Welding Fixtures
Welding fixtures are tools that hold and position workpieces during welding. They help keep the workpieces stable and aligned, which leads to better-quality welds. You can customize these fixtures to fit different shapes, materials, and welding methods, making them vital for efficient and consistent welding work.
Assembly Fixtures
Assembly fixtures are essential tools that help reduce manufacturing errors. They hold and position parts during assembly, ensuring that components align correctly. This process makes assembly more efficient and consistent. These fixtures can be simple jigs or complex systems, and they can adapt to different products and assembly needs. This adaptability helps create an error-free manufacturing process and ensures high-quality products.
What are Jigs?
Assembly fixtures are essential tools that help reduce manufacturing errors. They hold and position parts during assembly, ensuring that components align correctly. This process makes assembly more efficient and consistent. These fixtures can be simple jigs or complex systems, and they can adapt to different products and assembly needs. This adaptability helps create an error-free manufacturing process and ensures high-quality products.
Types of Jigs
Template Jigs
Template jigs are manufacturing tools that ensure the consistent and accurate production of parts. They provide a precise reference surface or pattern to help position and align workpieces during machining, assembly, or inspection. By using template jigs, manufacturers can maintain tight tolerances, work more efficiently, and reduce errors, making them essential for modern manufacturing.
Plate Jigs
Plate jigs are tools used in manufacturing to hold and position parts during machining operations. They create a stable and precise surface, which helps ensure that parts are aligned correctly and meet size requirements. Industries like aerospace, automotive, and general engineering use plate jigs to maintain tight tolerances and ensure consistency.
Channel Jigs
Channel jigs are tools used in manufacturing to hold and position workpieces during machining. They help align and support parts with channels, grooves, or other complex shapes, ensuring accurate machining and improving product quality and efficiency.
Diameter Jigs
Diameter jigs are tools used in manufacturing to ensure parts are the right size and shape. They hold and position workpieces during machining, inspection, or assembly, helping to control the final product’s diameter accurately. Diameter jigs are essential for maintaining tight tolerances and high-quality standards in aerospace, automotive, and medical device manufacturing industries.
Leaf Jigs
Leaf jigs are specialized fixtures used in manufacturing, mainly metal and woodworking. They securely hold thin, flat workpieces, such as leaves or thin metal sheets, during machining. Leaf jigs provide a stable and precise platform to ensure consistent and accurate cuts, bends, or other modifications to the workpiece.
Ring Jigs
Ring jigs are tools used in manufacturing, especially in machining and metalworking. They hold and secure round or ring-shaped parts, like bearings and gears. Ring jigs provide a stable and accurate platform for these components, which helps with proper positioning and alignment and ensures consistent processing of the parts. They are essential for maintaining quality and efficiency when making circular or ring-shaped items.
Box Jigs
Box jigs are fixtures used in manufacturing to hold and position workpieces during fabrication. They provide a secure and repeatable clamping solution, ensuring parts are aligned accurately during machining, welding, or assembly. Box jigs have multiple clamping points and locating pins, which help handle parts efficiently and precisely. This design improves productivity and quality control in the manufacturing process.
Welding Jig
A welding jig is a tool that holds workpieces in the correct position and orientation during welding. It provides stability and support, which helps ensure consistent and high-quality welds. Welding jigs are essential in fabrication, assembly, and production areas where precision and repeatability are crucial.
What are the differences between jigs and fixtures?
Jigs and fixtures are essential tools used in manufacturing, but they have different purposes.
Jigs hold and guide a workpiece during tasks like drilling or milling. They help position the workpiece accurately and consistently, which leads to precise results.
On the other hand, fixtures hold a workpiece in place without guiding the tools used in manufacturing. They keep the workpiece stable and prevent movement during the process.
FAQs
Use our expertise in additive manufacturing and CNC machining to design and create custom jigs and fixtures that meet your needs. We focus on delivering high-quality solutions tailored to your requirements.
Jigs and fixtures improve manufacturing processes by making them more accurate, consistent, and efficient. They also help with precise positioning and support, streamlining operations.
Jigs and fixtures are vital tools in manufacturing. They help position parts accurately and consistently, boosting efficiency and improving quality.
Materials such as aluminum, stainless steel, and engineered plastics are standard in jigs and fixtures.