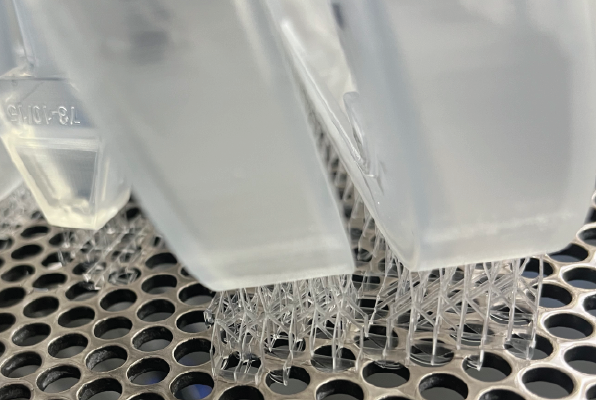
3D printing has changed how things are made by allowing for complex designs. One crucial but often ignored part of 3D printing is 3D-printed support structures. This blog post will explain what 3D-printed supports are and why they are essential for successful 3D printing projects.
What are supports in 3D printing?
Supports, the unsung heroes of 3D printing, play a crucial role in ensuring the stability of your printed parts during the intricate process. They are the key to supporting overhanging features, bridges, and complex shapes, thereby assuring successful prints. Our team of experts, with their unparalleled knowledge and experience, can guide you in using supports effectively to create high-quality, functional 3D-printed parts for your manufacturing needs, instilling confidence in your 3D printing projects.
What 3D printing technologies require supports?
3D printing technologies such as stereolithography (SLA), digital light processing (DLP), hybrid photosynthesis (HPS), fused filament fabrication (FFF), and material jetting all have one thing in common: the need for support structures. These supports guard complex shapes and overhangs, preventing them from collapsing or bending during printing. Without them, the potential for print failure is high, underscoring the importance of meticulous planning when designing parts for these methods, including the strategic placement and subsequent removal of supports.
3D printed supports in SLA, DLP, and HPS
Support structures are crucial in additive manufacturing, whether utilizing stereolithography (SLA), digital light processing (DLP), or hybrid photosynthesis (HPS). These supports are necessary because of the characteristics of the liquid resin and the build platform.
In stereolithography, support structures stabilize overhanging parts and prevent warping or distortion during curing. They provide the stability and strength required for parts to emerge from the resin vat accurately.
In digital light processing and hybrid photosynthesis, support structures help maintain the shape of 3D-printed models. They counteract forces during the build, ensuring the parts remain true to their intended shape and size.
Optimizing Designs to accommodate supports.
When designing for photopolymer 3D printing, you must consider the support structures that help create complex shapes. Here are some essential tips:
- Adjust the part’s orientation to reduce overhanging features.
- Add support points and lattice structures in strategic places.
- Use breakaway supports to make removal easy after printing.
- Optimize the density and placement of supports to save material.
- Consider shrinkage and warping, which can happen during the curing process.
3D printed supports in FFF
Fused filament fabrication (FFF) is a 3D printing method that uses plastic filament. The printer heats the filament and extrudes it onto a build surface, which cools and hardens to create layers.
Each layer comprises heated filament threads that stick to the previous layers. FFF can build shapes with vertical angles up to 45 degrees. If an overhang exceeds this angle, it may sag and ruin the print, so support structures are needed.
FFF fuses two main types of support: a flat accordion or lattice structure, which is common and works well for most parts, and tree-like support, which makes less contact and can improve the finish after processing. Operators usually choose the best support type to reduce any cosmetic effects on the design.
Optimizing designs to accommodate supports.
When designing fused filament fabrication (FFF) parts, consider the support structures you need during printing. Here are some tips to help you with your design:
- Minimize Overhangs: Change the part’s shape and position on the build plate to reduce overhanging features needing support. Surfaces that angle less than 45 degrees don’t need extra support.
- Use Support-Friendly Features: To use less support material, add design elements like chamfers, fillets, and tapered walls.
- Choose Easy-to-Remove Supports: You can easily remove support structures, like breakaway supports or water-soluble materials.
- Position Support Anchors Wisely: Place support points where they touch the part less, making them easier to remove.
- Test Support Settings: Try different support options, such as density, pattern, and air gaps, to find the right balance between firm support and easy removal.
- Plan for Finishing Touches: After printing, consider sanding or machining to smooth the surface and remove any marks left by supports.
3D printed supports in Material Jetting
Material jetting technologies, like Stratasys PolyJet and 3D Systems MultiJet Modeling, are similar to inkjet printers. Instead of using ink, these 3D printers layer liquid photopolymer on a build tray and use UV light to cure it.
Support material is needed to support any overhanging features. This material can be water-soluble or removed with pliers, water jetting, or sandblasting. Unlike fused filament fabrication (FFF), these supports do not affect the part’s appearance or quality, so it is hard to notice where the location of the supports after finishing it.
Optimizing designs to accommodate supports.
When designing material jetting parts, you must consider the support structures required for complex shapes. Here are some essential tips:
- Reduce overhanging features that require a lot of support. Change the part’s orientation to minimize these areas.
- Add channels or openings to make it easier to remove the support material.
- Use lattice or tree-like support structures, which are easier to remove than solid ones.
- Include support interface layers to help separate the part from the supports cleanly.
- Find the proper placement and density for supports to balance part stability with easy removal.