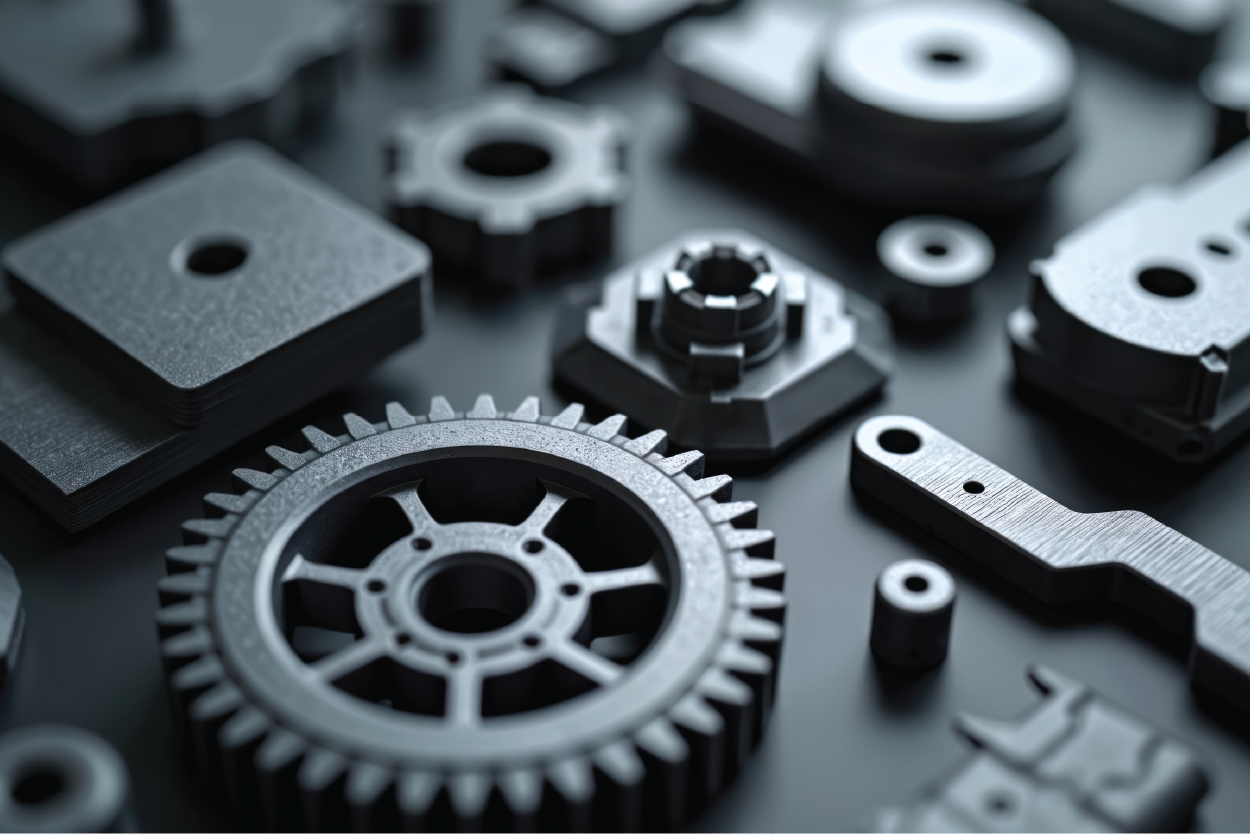
Composite materials, with their versatile applications, are revolutionizing industries globally. These materials, known for enhancing designs and performance, are particularly impactful in the aerospace and renewable energy sectors.
Recent advancements include using nanocomposites to enhance properties, applying advanced manufacturing techniques like 3D printing, and developing more substantial matrix materials.
Let’s explore these innovations in composite materials and their effects on various industries.
What is a composite?
Composites, with their adaptability and versatility, are materials that combine two or more different substances to enhance their properties. They usually include a reinforcing material, like fibers or particles, placed in a matrix material such as plastic, metal, or ceramic. This mix makes composites stronger, stiffer, and more valuable than the individual materials alone, creating many opportunities for innovation and design.
A short history of composites.
Composites, with their rich and significant history that spans thousands of years, connect us to our past and inspire us for the future. They started with simple materials, like mud bricks with straw, and have evolved into advanced products like carbon fiber and epoxy laminates. This history is a testament to the enduring power of human innovation and the potential of these materials to help us create new things.
Since ancient times, people have mixed materials to make more potent products. Civilizations like the Babylonians, Egyptians, and Chinese used basic composites for building and making weapons. Over time, new materials and better manufacturing methods led to more innovations.
Today, composites are crucial in many industries, including aerospace, automotive, sports equipment, and renewable energy. They are lightweight, strong, resistant to corrosion, and flexible in design, changing how we manufacture and engineer products and offering reliable solutions for various needs.
The future of composites is promising, with continuous improvements in materials and processing methods. These advancements, such as new reinforcing fibers, robust matrix materials, and innovative processing methods like machining, fabrication, and 3D printing, will continue to shape the products and technologies of tomorrow.
Properties of Composite Materials.
Composite materials have improved the manufacturing industry by providing unique advantages that affect many sectors. Prototek Digital Manufacturing, a leader in digital manufacturing solutions, is eager to discuss these materials and their properties. We are here to help our clients take full advantage of these benefits and use the unique features of composite materials effectively.
Strength and Durability
Composite materials are strong yet lightweight, making them great for weight-reduction projects. Their layered structure lets us adjust strength and stiffness based on specific needs, ensuring they are durable and reliable.
Corrosion Resistance
Composite materials resist corrosion and can handle harsh weather and chemicals. This property makes them a good choice for places where traditional materials may fail. Their durability helps components last longer and lowers maintenance and replacement costs.
Design Flexibility
Composite materials are flexible and allow for custom designs, which helps engineers and manufacturers create innovations. These materials can form complex shapes and combine multiple functions seamlessly.
Thermal and Electrical Properties
The design of composite materials meets specific needs for heat resistance and electrical conductivity based on the materials used. These properties help components handle extreme temperatures, provide insulation, or conduct electricity effectively.
At Prototek Digital Manufacturing, we focus on helping our clients unlock the benefits of composite materials and effectively use their unique properties.
10 Types of Composites
Based on the materials used, there are different types of composites. Each type has specific physical and mechanical properties that suit various uses.
Nanocomposites
Nanocomposites are materials that mix tiny particles with a base material, such as nanoparticles, nanofibers, or nanotubes. This mixture improves the properties of the composite. Nanocomposites perform better using these tiny materials’ strong mechanical, thermal, electrical, and optical features. Many industries use these composite materials, including aerospace, automotive, and electronics.Nanocomposites are advanced materials that combine nanoscale materials, such as nanoparticles, nanofibers, or nanotubes, with a matrix material to create a composite with enhanced properties. These unique materials leverage the exceptional mechanical, thermal, electrical, and optical characteristics of nanomaterials to improve the overall performance of the composite. Nanocomposites offer a wide range of applications across industries, including aerospace, automotive, electronics, and beyond.
Metal Matrix Composites (MMCs)
Metal Matrix Composites are unique materials made from a metal base combined with extra parts, either ceramic or metal. The metal base is usually aluminum, magnesium, or titanium. It provides strength, flexibility, and good thermal or electrical conductivity. The added parts boost important features like stiffness, strength, wear resistance, and heat stability. Because of these qualities, many industries, such as aerospace, automotive, and manufacturing, use MMCs.
Polymer Matrix Composites (PMCs)
Polymer Matrix Composites (PMCs) are strong, durable materials that combine polymers, fibers, or particles. They are versatile and have many uses. At Prototek Digital Manufacturing, we make high-quality PMC parts using advanced methods like additive manufacturing and CNC machining. If you need custom PMC components or support for your project, our team is here to help.
Glass Fiber Reinforced Polymers (GFRPs)
Glass Fiber Reinforced Polymers are strong, durable materials made from glass fibers and plastic resins. They are lightweight, resist corrosion, and allow for flexible design. At Prototek Digital Manufacturing, we use our skills in 3D printing, CNC machining, and other methods to create high-quality GFRP parts that meet our clients’ specific needs.
Hybrid Composites
Hybrid composites are materials made by combining two or more types of reinforcement within one matrix. This combination improves specific properties and overall performance. By using the strengths of different reinforcement materials, hybrid composites perform better than traditional composites, which use only one type of reinforcement.
Natural Fiber Composites (NFCs)
Natural Fiber Composites are materials made with natural fibers from plants or animals. These composites offer a sustainable and eco-friendly choice compared to traditional synthetic materials. NFCs are lightweight, biodegradable, and renewable, making them useful for many applications, such as cars, buildings, and consumer products. By taking advantage of the strengths of natural fibers, NFCs can help reduce the environmental impact of manufacturing while still providing good mechanical and physical properties.
Ceramic Matrix Composites (CMCs)
Ceramic Matrix Composites are strong materials that combine ceramics and reinforcing fibers. They can handle high temperatures, resist corrosion, and endure harsh conditions.
A CMC has a ceramic base, like silicon carbide or alumina, reinforced with fibers from the same materials. This combination makes CMCs very strong, stable in heat, and resistant to wear. Because of these properties, CMCs are great for use in aerospace, automotive, and industrial fields.
Carbon Reinforced Polymers (CFRPs)
Carbon-reinforced polymers (CFRPs) are strong, lightweight materials that combine carbon fibers with plastic. They have excellent strength and stiffness, making them popular in the aerospace, automotive, and sports equipment industries. CFRPs are known for their high strength-to-weight ratio, rust resistance, and customization ability, making them an excellent choice for weight reduction projects while maintaining firm and stable structures.
Aramid Fiber Reinforced Polymers (AFRPs)
Aramid Fiber Reinforced Polymers (AFRPs) are strong materials that combine aramid fibers with flexible polymers. Due to their unique strengths, these materials are popular in the aerospace, automotive, and defense industries.
AFRPs are known for being tough, resistant to impacts, and stable at high temperatures. They are ideal for reducing weight while maintaining essential strength. Through adjustable features and design, AFRPs are expanding the possibilities of manufacturing and engineering.
Functionally Graded Composites (FGCs)
Functionally Graded Composites (FGCs) are unique materials that gradually change composition and structure. This feature allows for adjusting their properties, like thermal, mechanical, or electrical features, to fit specific needs. FGCs perform better and offer more functions than traditional materials. Because of this, they are helpful in many fields, including aerospace, automotive, and biomedical engineering.
Common Applications for Composites
Composite materials combine two or more different materials. Together, they form a new material that is often stronger, more durable, and more flexible than the individual ingredients. Because of these unique properties, many industries use composites. Here are some typical applications.
Aerospace and Aviation
Composites are widely used in aerospace and aviation because they are strong yet lightweight. You can find them in aircraft parts like fuselages, wings, tail sections, and engines. These materials help make planes lighter and more fuel-efficient. Composites also resist corrosion and last longer than traditional metal materials.
Automotive
In the automotive industry, manufacturers use composites to reduce vehicle weight and improve fuel efficiency. Composites are found in parts like body panels, chassis, and interiors, providing better strength and flexibility. They also resist corrosion and allow fewer parts, making manufacturing more efficient.
Renewable Energy
Composites are key in renewable energy, especially wind turbine blades. Their lightweight and strong nature allows for longer and more efficient blades, which improves wind turbines’ overall performance. Solar panels and tidal energy equipment use composites.
Marine and Shipbuilding
Composites are widespread in marine and shipbuilding due to their resistance to corrosion and lightweight nature. They are used in boat hulls, decks, and other marine parts, improving performance, reducing maintenance, and increasing fuel efficiency.
Infrastructure and Construction
Infrastructure and construction commonly use composites. They offer greater strength, durability, and corrosion resistance than traditional materials, making them a good choice for long-lasting projects that require minimal upkeep.
FAQs
A composite is a material made by combining two or more different components. Typically, it includes a reinforcing material and a matrix, creating a stronger and more durable product.
Composites are strong, lightweight, and flexible in design. However, they can cost more and need unique manufacturing processes.
Composites consist of two or more materials. They usually have a reinforcing fiber and a matrix material that work together to improve strength and durability.
The most common fibers in composites are carbon, glass, aramid, and natural fibers.
Composite materials may have a higher upfront price, but their durability and customization can make them cost-effective. The benefits usually outweigh the initial cost.
Standard methods for making parts with composites include compression molding, resin transfer molding, filament winding, and automated fiber placement. These techniques help produce complex, high-performance composite components.