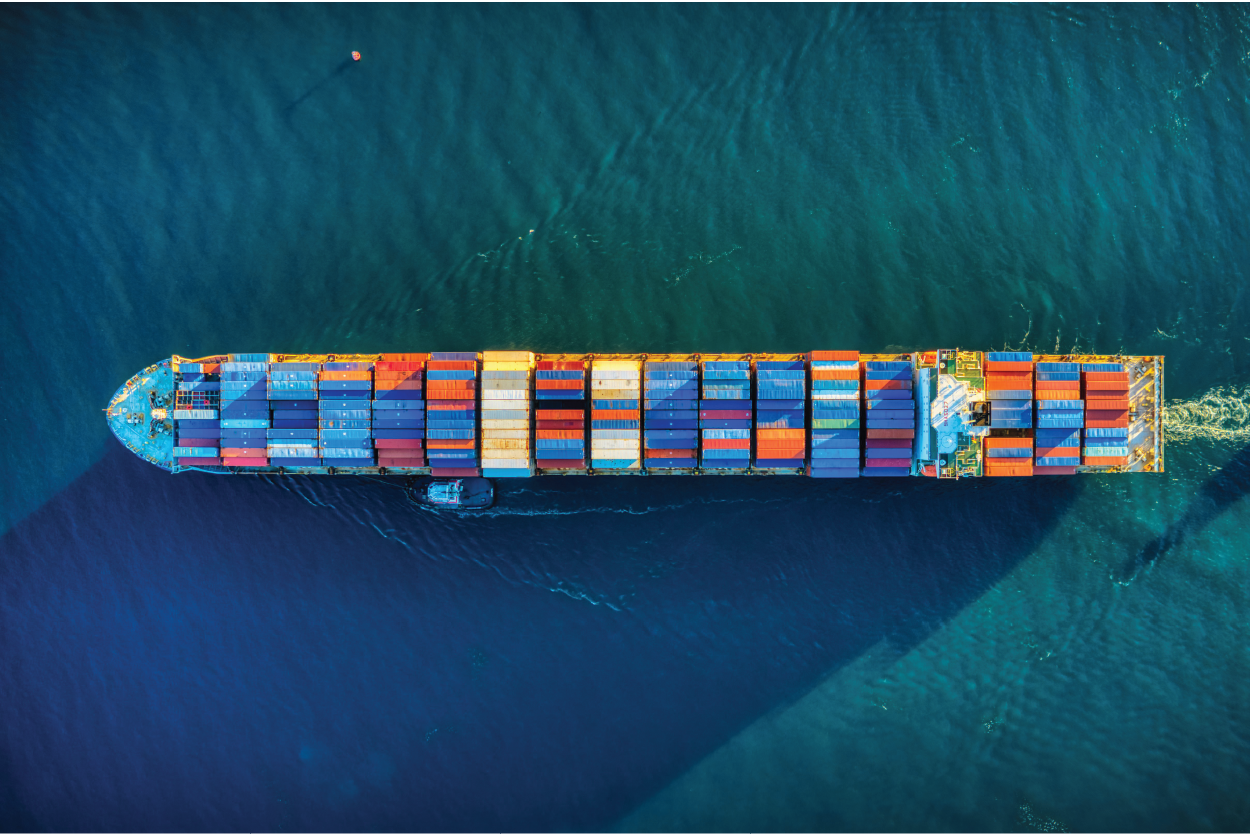
Manufacturing technologies for shipbuilding and making parts for ships are an integral part of the maritime industry. This process uses different methods, materials, and technologies to ensure that boats can handle harsh conditions at sea.
This blog post will examine the main components of ship parts manufacturing. We will cover the materials used, the manufacturing processes, and the importance of quality control.
A glimpse of the history of Shipbuilding in the United States
The United States has a long history of shipbuilding. American shipbuilders have helped strengthen the country’s maritime power from the colonial era to today. It is a legacy that we can all be proud of.
Shipbuilding in the U.S. began in the 1600s when European settlers made simple fishing and trading boats to travel along rivers and coastlines. As the colonies grew, the shipbuilding industry expanded, especially in Massachusetts, Pennsylvania, and Maryland.
The American Revolution was a key moment for shipbuilding. The new United States aimed to strengthen its naval power. Shipbuilders like Joshua Humphreys created the “six frigates,” which helped the U.S. Navy win battles against the British. During this time, clipper ships, known for their speed and efficiency, were also developed.
The 1800s were a golden age for American shipbuilding. New technology in steam power, steel, and design changed the industry. Iconic ships like the USS Constitution and the RMS Titanic were built during this time, showcasing the skills of American shipbuilders.
Today, shipbuilding is crucial for the U.S. economy and military. Shipbuilders create advanced aircraft carriers and modern commercial ships, continuing the proud tradition of American shipbuilding in the global maritime space.
Understanding Ship Parts and Systems
Ships have many parts, each with a specific function. These parts fall into three categories: structural components, mechanical systems, and electrical systems.
- Structural components include the hull, deck, and bulkheads.
- Mechanical systems cover engines, propellers, and pumps.
- Electrical systems involve wiring, lighting, and navigation equipment.
Every part of a ship, from the hull to the electrical systems, is crafted precisely to ensure the vessel’s safety and efficiency. This commitment to quality is a cornerstone of the shipbuilding industry, reassuring all who rely on these vessels.
Materials Used in Manufacturing for Shipbuilding
Shipbuilding is a complicated process that requires many unique materials to create vessels of all sizes. At Prototek Digital Manufacturing, we know how important these materials are for building and operating ships.
Steel: The Strong Choice for Shipbuilding
Steel is the primary material in shipbuilding. It is strong, durable, and resistant to corrosion. Most modern ships use steel for their hull and superstructure because it provides the necessary strength to survive the challenges of the open sea.
Aluminum: Lightweight and Flexible
Although steel is a standard material used in shipbuilding, aluminum is a good alternative for smaller vessels and fast boats. Aluminum is lightweight, improving fuel efficiency and allowing for greater cargo capacity while still strong.
Plastic: Insulating and Corrosion Resistant
Plastic materials are necessary in shipbuilding because they are flexible and essential. They help create lightweight, substantial parts, like piping systems, and provide sound insulation for sensitive electronics. Their corrosion resistance is helpful in marine environments, where traditional materials can break down quickly due to saltwater and harsh conditions. Using advanced plastics improves ship performance and reduces maintenance costs, showing the industry’s focus on innovative solutions.
Composite Materials: The Next Step in Shipbuilding
Composite materials, like fiberglass-reinforced polymers (FRP) and carbon fiber-reinforced polymers (CFRP), are becoming more common in shipbuilding. These materials are strong, lightweight, and corrosion-resistant, making them suitable for high-performance yachts and military ships.
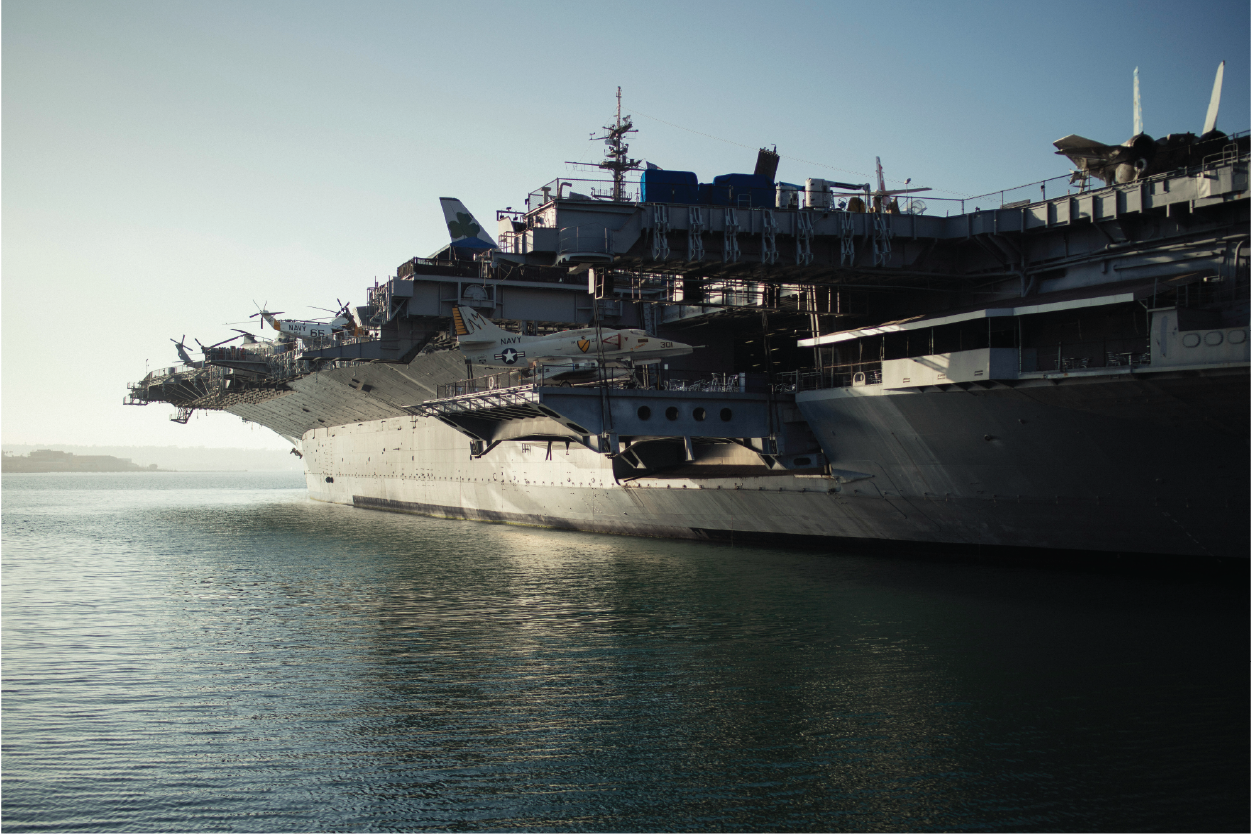
Manufacturing Technologies for Shipbuilding
The manufacturing of ship parts involves several key processes:
3D Printing in Shipbuilding
Quick Prototyping
3D printing allows shipbuilders to make prototype parts quickly, speeding up design changes and testing. Fast design updates are essential in the maritime industry because they can affect performance and safety.
On-Demand Spare Parts
3D printing enables shipbuilders to create spare parts as needed. This method of manufacturing components is advantageous because traditional supply chains can often be slow. By printing parts on demand, shipbuilders can reduce inventory costs and minimize repair downtime.
Lightweight Structures
With 3D printing, shipbuilders can create lightweight structures that are strong and durable. Lightweight is essential for naval vessels, improving fuel efficiency and overall performance.
Customization
3D printing makes it easy to customize parts for specific vessels. This ability to create tailored components can improve functionality and performance.
Applications of CNC Machining in Shipbuilding
Hull Manufacturing
CNC machines cut and shape large hull sections very accurately. This accuracy helps ensure the hulls meet design specifications and performance standards, reduce structural issues, and improve seaworthiness. With advanced CNC technologies, shipbuilders can create complex shapes that enhance hydrodynamics, improving fuel efficiency and speed.
Component Production
Shipbuilders use CNC processes to make vital components like brackets, engine mounts, and structural parts. These machines use materials, including metals and composites, to create sturdy yet lightweight parts. CNC machining produces components to exact specifications, reducing inconsistencies and the need for rework.
Propeller and Shaft Manufacturing
Making high-precision components like propellers and shafts is essential for a ship’s performance. CNC machining allows for detailed profiles and smooth finishes that help achieve good propulsion efficiency. These parts undergo thorough testing for balance and durability to ensure they can handle harsh marine conditions.
Interior Fittings
CNC technology also helps create customized interior ship fittings, such as furniture and control panels. With advanced design software, shipbuilders can make attractive, functional interiors that meet clients’ needs. It improves the passenger experience and better uses space within the vessel.
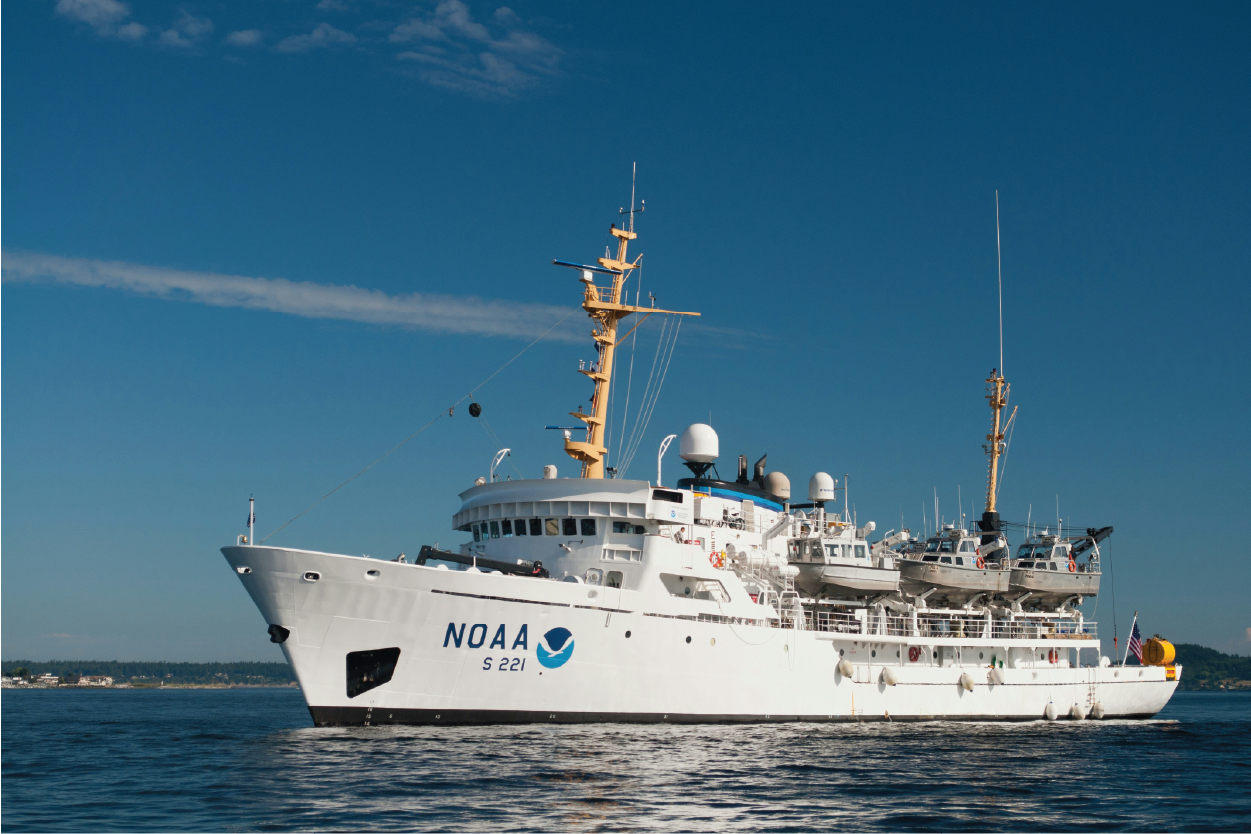
Applications of Sheet Metal Fabrication in Shipbuilding
The Hull
The hull is a ship’s leading body for strength and performance. Made from strong materials like steel or reinforced fiberglass, it can handle harsh sea conditions, such as strong waves, currents, and saltwater.
The hull’s design helps it stay afloat and stable, allowing the ship to navigate safely in different sea conditions. If designed well, it can reduce drag, which improves fuel efficiency and makes the ride more comfortable for passengers.
Decks and Superstructures
Decks and superstructures are crucial for a ship’s operation and safety. Sheet metal makes these features, including deck plates that provide walkable surfaces. Bulkheads are vertical walls that separate different areas of the ship and strengthen its overall structure.
Engine and Machinery Components
Sheet metal is essential for many parts of engines and machines. It makes enclosures that protect engines and reduce noise, making things safer. Fabricated mounting brackets from sheet metal hold engines and equipment securely, ensuring they stay stable while operating. These components work together to improve the efficiency and effectiveness of machinery.
Exhaust Systems
Exhaust systems are essential for controlling emissions and helping the engine run efficiently. They are mainly made from sheet metal and contain key parts like exhaust ducts and mufflers. Exhaust ducts move harmful gases away from the engine, while mufflers reduce noise and help control emissions. Both parts use durable sheet metal to handle the demanding conditions of the exhaust environment.
Storage Tanks
Ships need storage tanks for fuel, water, and other essential supplies. Sheet metal plays a vital role in making these tanks. We use thick sheets for fuel tanks to ensure they are strong and safe. Water tanks are custom-made to fit specific spaces in the ship, which helps make the most of the available room.
Safety Features
Safety is paramount in shipbuilding. Sheet metal helps improve many safety features. One key use is lifeboat frames, which strongly support lifeboats and safety gear. Sheet metal is also critical for making guardrails and barriers that keep the crew safe while moving on deck. These structures add to the vessel’s safety and create a secure working environment for everyone on board.
HVAC Systems
Heating, Ventilation, and Air Conditioning (HVAC) systems are vital for comfort on ships. A key material in these systems is sheet metal, which serves important purposes.
First, sheet metal makes ductwork that moves conditioned air throughout the ship. Well-designed ducts ensure good airflow, creating a stable and comfortable environment for the crew and passengers.
Second, the chassis is built with sheet metal and supports the holding of the HVAC equipment. These supports provide stability and help the HVAC systems function effectively during a voyage.
Importance of Quality Control in Shipbuilding Manufacturing
Quality control (QC) is significant in shipbuilding. It affects safety, performance, and reliability.
Safety and Risk Management
Shipbuilding involves complex structures that need to withstand harsh marine conditions. Quality control ensures that all parts meet strict safety standards, reducing the risk of failure during operation.
Compliance with Standards
The shipbuilding industry must follow various regulations and standards. Reasonable quality control ensures that all parts comply with these rules. It not only protects the manufacturer but also keeps the vessel and its crew safe.
Prevention of Defects
Quality control includes thorough testing and inspection of parts to catch defects early. This process helps maintain high standards and prevents defects that could harm the ship’s integrity.
Cost Efficiency
Quality control can save costs by reducing waste and rework. Finding defects early helps companies avoid expensive repairs or replacements. This is especially important in shipbuilding, where delays and repairs can be costly.
Building Trust and Reputation
High-quality standards build trust between manufacturers and clients. A strong reputation for quality leads to repeat business and referrals, which are essential in the competitive shipbuilding market.
Are you ready to start your project?
FAQs
Shipbuilding is the construction and repair of ships, boats, and other watercraft.
Shipbuilding hubs located in coastal states like Maine, Mississippi, and California.
Additive manufacturing, CNC machining, and sheet metal fabrication.
Shipbuilding materials commonly include steel, aluminum, fiberglass, and composite materials. These durable and versatile materials are essential for constructing strong, lightweight, and corrosion-resistant vessels.