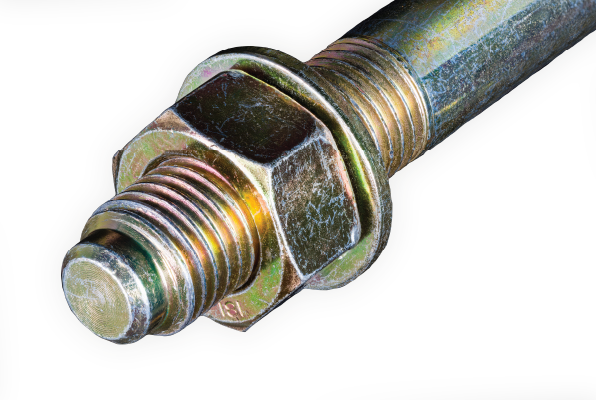
Which Conversion Coating is Ideal for Your Project?
Selecting the appropriate conversion coating is crucial for improving the performance and durability of metal surfaces in your projects. There are several types available, including phosphate, chromate coatings, anodizing, and black oxide. Each type provides distinct advantages suited to specific metals and applications. Whether you work in the automotive, aerospace, or electronics industries, gaining a thorough understanding of these coatings can greatly influence the success of your project.